Not Your Typical Compost Feedstock
Aspen Skiing Company: Compost Feedstock
EPA530-F-03-022
July 2003
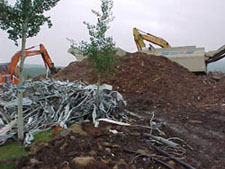
In Aspen, Colorado, snow is not the only material piling upconstruction and demolition (C&D) debris is being generated nearly as fast as the snow falls. Thats why environmentally conscious Aspen Skiing Companywhile welcoming the snowhas decided to reuse building materials and create compost out of the remaining materials instead of throwing them away.
When it was time for the Aspen Skiing Company to demolish two buildings in 1999, the company chose to institute a deconstruction programreversing the building process and removing and sorting reusable items instead of sending the waste to the landfill. The Aspen Skiing Company ground up the remaining sheetrock and scrap lumber, turning it into compost. Using this approach, the company kept 84 percent of the old buildings out of the local landfill and allowed the materials to have a second life in new buildings and compost.
Auden Schendler, director of environmental affairs for the company, said, Although deconstruction may cost more, it has proved to be successful, and the environmental benefits are clear.; The only real challenge the company faced prior to initiating the program was identifying a contractor willing to train the laborers to deconstruct rather than demolish.
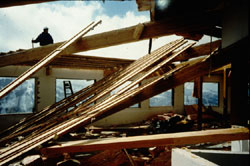
The most significant environmental benefit of deconstruction is the potential to recycle or reuse materials. The Aspen Skiing Company brought the sheetrock and wood to the local landfill where it was collected for composting. The compost generated is combined with wastewater treatment sludge from other districts and is used for applications such as highway maintenance.
Significant cost savings is a huge draw for deconstruction. For example, by deconstructing its Sundeck Restaurant, the Aspen Skiing Company realized significant cost savings. Normally, there is a standard tipping fee of $21.50 per cubic yard on C&D waste, but the landfill manager waived it because he was able to sell the compostsaving the Aspen Skiing Company over $42,000 in avoided disposal costs. Schendler suggests negotiating contractors fees down by accounting for the reduced landfill fees, as long as the cost savings can be proved. Otherwise, the contractor can capture the cost savings, as was the case with the second deconstruction project at Aspen.
For more information, see the Aspen Skiing Companys environmental programs website.
View and print this fact sheet (PDF) (1 pg, 171K, about PDF)
Disclaimer: Reference herein to any specific commercial products, process, or service by trade name, trademark, manufacturer, or otherwise, does not necessarily constitute or imply its endorsement, recommendation, or favoring by the United States Government. The views and opinions of authors expressed herein do not necessarily state or reflect those of the United States Government, and shall not be used for advertising or product endorsement purposes.