Iron and Steel
Note: EPA no longer updates this information, but it may be useful as a reference or resource.
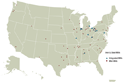
Map showing location of U.S. facilities in this sector; please click on the map to see a larger version.
Sector Profile
The Iron and Steel sector covers the manufacture of steel into basic shapes and forms that then can be used to create products. The sector is divided into two basic types of production that each represents approximately half of domestic production. Integrated steel mills use a three-step process to produce steel from coal, involving cokemaking, ironmaking (using a blast furnace), and Basic Oxygen Furnace (BOF) technology. Alternatively, "mini-mills" produce steel from metal scrap using Electric Arc Furnace (EAF) technology, without operations for coking or ironmaking.
Coke, which is the fuel and carbon source at integrated mills, is produced by heating coal in the absence of oxygen at high temperatures in coke ovens. Pig iron is then produced by heating the coke, iron ore, and limestone in a blast furnace. In a BOF, molten iron from the blast furnace is combined with flux and scrap steel where high-purity oxygen is injected. This process—with cokemaking, ironmaking, steelmaking, and subsequent forming and finishing operations—is referred to as “fully integrated production.” Alternatively, in an EAF the input material is primarily scrap steel, which is melted and refined by passing an electric current from the electrodes through the scrap.
The percentage of steel produced by EAFs is significant and growing. In 2001, 125 minimills generated 47.5 percent of the steel produced domestically, consuming 75 million tons of ferrous scrap to do so. Nearly 200 mills make up this sector, employing more than 150,000 people. The mills are concentrated geographically in Great Lakes states, although the South also has a large number of mini-mills. Principal consumers of the steel generated from these mills are auto manufacturers and the construction industry.
The sector has multi-media impacts, including air emissions (CO, SOx, NOx, PM2), wastewater contaminants, hazardous wastes, and solid wastes. The major environmental impacts from integrated steel mills are from coking and ironmaking, although U.S. steelmakers are turning to new technologies to decrease the sources of pollution from, and their reliance on, coke.
As an industry, mini-mills are the largest U.S. consumers of recycled steel scrap, but also face issues related to contaminants in scrap products. The energy used by mini-mills generates greenhouse gas emissions from power generation. An emerging trend to generate heat on-site by burning carbon will improve energy efficiency but will also increase emissions.
Performance Data and Trends for this Sector
You can read the Iron and Steel chapter in the of the most recent Sector Performance Report.
The Iron and Steel chapter in Energy Trends in Selected Manufacturing Sectors: Opportunities and Challenges for Environmentally Preferable Energy Outcomes (PDF) (142 pp, 342K, About PDF) outlines the trends and opportunities in energy use for this sector.
Mercury Switch Recovery Program
The Mercury Switch Recovery Program is the result of a two-year partnership with EPA programs, environmental organizations, the Environmental Council of the States, and several industry trade associations. Two trade associations—the American Iron and Steel Institute and the Steel Manufacturer Association—are among the participating entities.
This national initiative, begun in 2006, will help cut mercury air emissions by up to 75 tons over the 15-year span of the project. The National Vehicle Mercury Switch Recovery Program is removing mercury-containing light switches from scrap vehicles before the vehicles are flattened, shredded, and melted to make new steel. The program is also providing a financial incentive for those who remove mercury switches. Together with existing state mercury switch recovery efforts, this program will significantly reduce mercury air emissions from the furnaces used in steel making—the fourth leading source in the United States after coal-fired utility boilers, industrial boilers, and gold mining.
The goal of the program is to collect 80 to 90 percent of available mercury switches by 2017. Click here to see up-to-the-minute recovery numbers.
For more information, please go to:
- The National Vehicle Mercury Switch Recovery Program
- January 2009 fact sheet: Here's How Your Local Government Can Switch on a New Green Program (PDF) (1 pp, 47K, About PDF)
- August 2006 Fact Sheet: National Vehicle Mercury Switch Recovery Program
- End of Life Vehicle Solutions (ELVS)
- Outreach material for automobile and scrap recyclers (PDF) (2 pp, 666K, About PDF) (August 2008)
- Proper management of mercury switches in automobiles
Promoting Environmental Management Systems
EPA worked with the Steel Manufacturers Association (SMA) on a program of training and technical resources to help steelmakers implement environmental management systems (EMS). SMA members produce steel by melting scrap metal and other iron-bearing materials in electric arc furnaces. These steel "mini-mills" produce more than half of all new U.S. steel, mostly by recycling scrap steel. The comprehensive environmental management approach taken with an EMS provides a sound framework for pursuing improved environmental performance.
EPA and SMA developed technical tools to increase EMS use within the industry. An EMS implementation guide outlines the essential elements of an EMS, gives detailed guidance on satisfying each element, and highlights examples from the steelmaking industry.
Iron and Steel Sector Environmental Management System Implementation Guide for Electric Arc Furnace Operators:
- 01 TOC and Introduction.pdf (PDF) (12 pp, 183K, About PDF)
- 02 Section I.pdf (PDF) (36 pp, 357K, About PDF)
- 03 Section II Tiers I-III.pdf (PDF) (98 pp, 610K, About PDF)
- 04 Section II Exhibits.pdf (PDF) (38 pp, 416K, About PDF)
- 05 Appendices.pdf (PDF) (11 pp, 102K, About PDF)
- Page13and14.pdf (PDF) (2 pp, 157K, About PDF)
- EMS guideTABS.pdf (PDF) (4 pp, 18K, About PDF)
- EMSguide_IronSteel_covFINAL.pdf/Cover page (PDF) (1 pg, 3MB, About PDF)
Resources
Trade Associations
American Iron and Steel Institute
1140 Connecticut Avenue, NW,
Suite 705 Washington, DC 20036
Tel: (202) 452-7180
Steel Manufacturers Association
1150 Connecticut Avenue, NW,
Suite 715 Washington, DC 20036-3101
Tel: (202) 296-1515
Key Documents
- Profile of the Iron and Steel Industry (1995) (PDF) (115 pp, 672K, About PDF) is several years old but provides a tremendously helpful overview and a lot of specific information.
Sector-related Links
- National Emission Standards for Hazardous Air Pollutants: Integrated Iron and Steel Manufacturing. This May 20, 2003 ruling promulgates national emission standards for hazardous air pollutants (NESHAP) for integrated iron and steel manufacturing facilities. The final standards establish emission limitations for hazardous air pollutants (HAP) emitted from new and existing sinter plants, blast furnaces, and basic oxygen process furnace (BOPF) shops.
- The Sector Facilities Indexing Project was discontinued in 2004, Most of the information found in SFIP can now be obtained in EPA's Enforcement Compliance History Online (ECHO). The ECHO Sector Facility Indexing Universe field provides compliance and inspection history and demographics information for the five SFIP industry sectors.
- The Department of Energy's Industries of the Future Program
presents a wealth of information on the steel industry, including its environmental impact.
- The EPA Municipal Solid Waste Program contains information on steel recycling activities.
- The U.S. Geological Survey tracks various iron and steel statistics, but also periodically generates a profile on the industry. The 2006 Yearbook (PDF) (115 pp, 672K, About PDF)
is the most up to date.
- EPA Effluent Guideline Rulemaking Process for Iron and Steel
- Industry Sector Notebook: Profile of the Iron and Steel Industry (1995) (PDF) (115 pp, 672K, About PDF)
- ELVS Mercury Switch Recovery Program