WasteWater Compliance Lean Kaizen Event
National Information
- EPA's National Pollution Prevention Homepage
- Basic Information
- Grants & Funding
- Laws and Policy
- Partnerships
Region 4 Toolkits
Resources
Contact Information
Pollution Prevention and Innovation Team
U.S. EPA Region 4
r4sustainability@epa.gov
Background
The Northeast District Wastewater Compliance is a section of the Florida Department of Environmental Protection that regulates more than 365 wastewater treatment facilities in Northeast Florida. Wastewater Compliance conducts more than 1,000 inspections per year of the treatment facilities to ensure compliance with applicable regulations.
After each inspection the Wastewater Compliance Section sends a letter to inform the facility if it is in compliance with state rules. If the facility is found to be out of compliance, a case is opened in a compliance status-tracking database, which is maintained by the Wastewater Compliance staff. Wastewater Compliance staff must ensure that each facility responds to this letter and fixes any compliance issues in a timely manner and in accordance with applicable rules and regulations, allowing them to close the case.
Problem Statement
Prior to the Lean event, there was no standard process for closing a case. Staff had individual methods for updating the database and it was difficult to obtain up-to-date information on which cases were open and required further response from the Wastewater Compliance Section.
Before the event, 708 cases had been open for more than 60 days. Furthermore, approximately five times per year, inspectors would encounter an open case of noncompliance that needs to be researched before they could re-inspect a facility. The Wastewater Compliance Section realized that it needed a standard process for staff to close a case as well as a faster case closure time in order to meet its environmental and quality goals.
Scope
Project Scope: The Kaizen event addressed the process of tracking each case from the time a letter is sent to a facility until the case is closed.
Project Team: Nine members, including a Team Leader and Champion.
Goal: Create a standard process that ensures all follow-up to an inspection is completed within 60 days.
Solutions Developed
The Lean Kaizen team mapped the current tracking process and surveyed it for steps that did not add value or information to the process of closing noncompliance cases. As a result of the event, the team created a standardized operating procedure for entering case data into the compliance database, tracking a case, and closing a case. Also, a standard procedure was established for tracking follow-up action items required for a facility to return to compliance and to close each case. Automated email reminders were setup to alert staff of a monthly inspectors’ meeting, which ensures the database is being updated.
All employees who were involved with inspection follow-up were trained in this new procedure.
Results
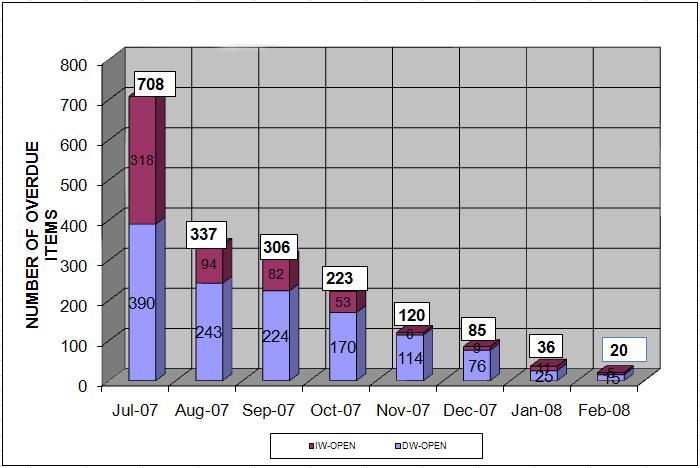
Time Saved: 452 hours per year, because inspectors did not need to check unclosed inspection files prior to re-inspecting facilitities.
Environmental: The number of cases open for more than 60 days dropped dramatically with more than a 90% improvement over the old system. This timely closure of cases improved wastewater treatment facilities’ compliance with state laws, protecting the environment and human health.
Cost Savings: $37,000
Other Benefits: The new system prevents follow-up items to inspections from being dropped or forgotten during employee turnover and allows managers to be confident that staff response to wastewater treatment facilities is prompt and accurate.
Contact Information
Tom Kallemeyn
Florida Department of Environmental Protection, Northeast District
Thomas.Kallemeyn@dep.state.fl.us